In machining, it is not the CNC machines that are the critical success factor, but the number of spindle hours per employee. ‘Many companies concentrate on machine autonomy, which is also very important, yet forget how many man-hours it takes to run a CNC machine for 6,000 hours on an annual basis,’ says Frank Biemans of BMO Automation. A valuable KPI to draw attention to this is the Operator Performance Ratio.
Spindle hours remain important, yet in times when staff shortages are the biggest bottleneck, companies often continue to invest in labour-intensive automation, such as pallet loading, for example. Or they fail to invest in CNC machines with a large tool changer, which means the operator spends hours each day changing tooling. The focus, believes Frank Biemans, founder of BMO Automation, should be on how many man-hours you need to invest in something to achieve a certain spindle hour output. By optimising this ratio, factory performance goes up tremendously. A valuable KPI to draw attention to this is the Operator Performance Ratio. The focus should lie on increasing this ratio.
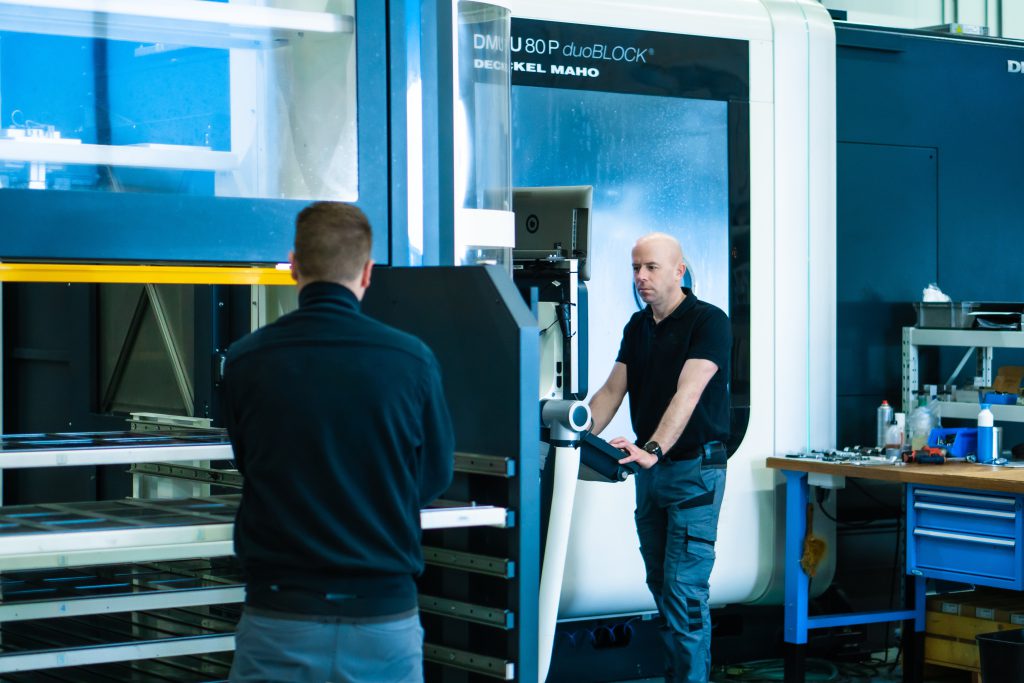
Too few skilled workers
Every production manager or owner of a manufacturing company is familiar with them: terms like TEEP (Total Equipment Effectiveness Performance) and OEE (Overall Equipment Effectiveness), KPIs that indicate how effectively machines are being used. Frank Biemans believes that in the current situation with labour shortages these concepts should be expanded to include how effectively employees are deployed: the OPR (Operator Performance Ratio). Machines and equipment can be bought or leased, but skilled workers are not easy to find. The lack of CNC operators and programmers is currently causing stagnation among suppliers. Especially in the machining industry, the work is there, but companies cannot meet the demand because they have too few skilled workers.
Higher productivity CNC machine with same man-hours
The Operator Performance Ratio is a KPI that companies use to calculate how the number of spindle hours relates to the number of operators. They can use this metric to start working towards more spindle hours with the same number of operators. ‘This is the solution to the staff shortages,’ says Frank Biemans. The calculation is simple: divide the number of spindle hours by the total number of man-hours (including set-up times and the hours it takes to load a robot cell) and the result is the OPR. If a day-shift operator operates one CNC machine that achieves 30 spindle hours in a week, the OPR is 0.75. If the CNC machine produces 90 spindle hours in the week based on a 3-shift system, the OPR remains 0.75. Having an operator set up the CNC machine during the day (40 hours) so it can run unattended for 120 spindle hours in the week, results in an OPR of 3. In other words, four times the output of the one-man, one-machine business. ‘It’s about productivity versus the man-hours you have to put in,’ says Frank Biemans. Increasing the number of spindle hours while working with the same number of operators brings down the hourly rate. After all, personnel costs are the biggest expense in most companies. A lack of skilled workers puts the brakes on the organisation’s growth. ‘Putting people where they add the most value and automating the rest results in the best performance,’ says Frank Biemans.
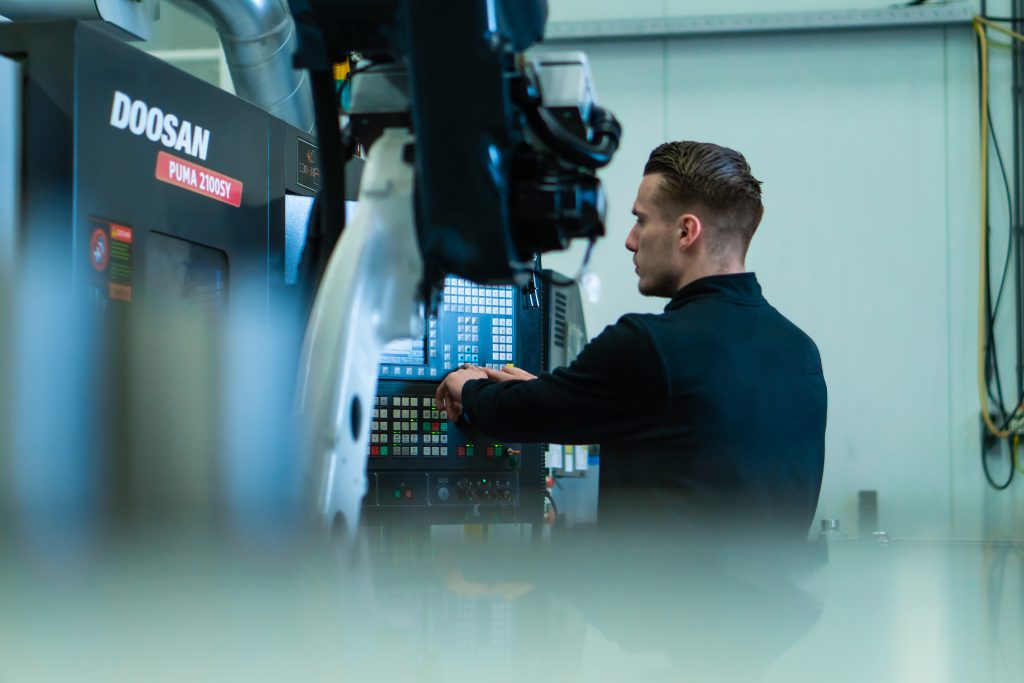
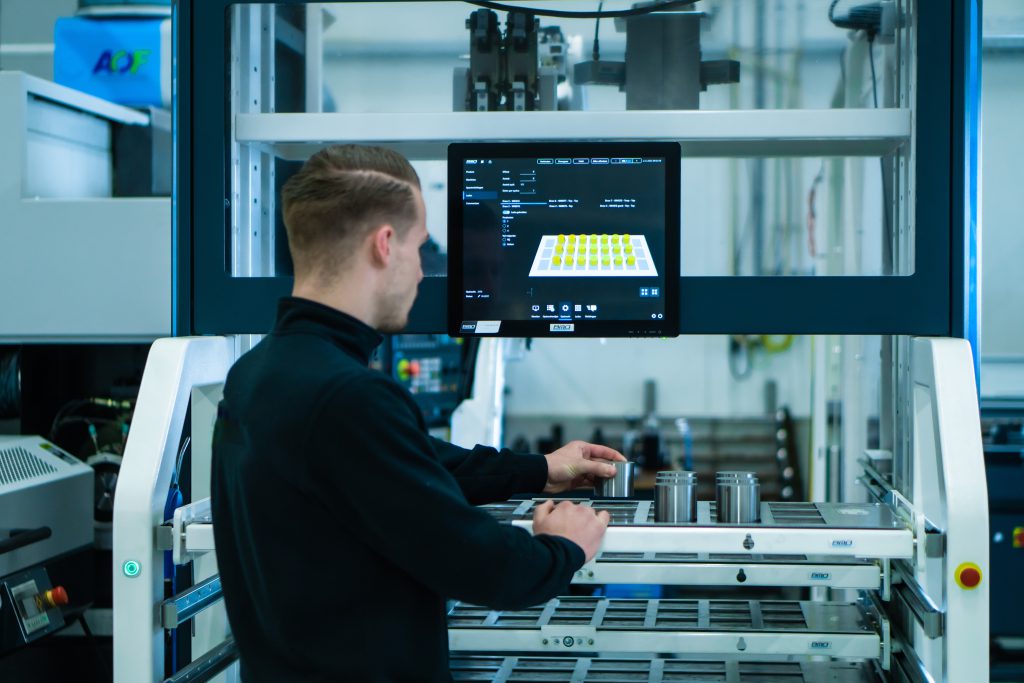
More output with Multi-Batch automation
He is convinced that machining companies in Europe can get much more output from their current machine and personnel capacity. Multi-batch automation like BMO Automation makes possible with its robotic cells is a good first step. BMO combines pallet and product handling for unmanned production of small batches of different products. ‘But even then, we see companies failing to keep the machine running all night,’ says Biemans. This is partly due to the long set-up times. Lack of standardisation, in terms of both tools and materials, is a factor that stands in the way of all-night of unmanned operation. ‘We can all be connected and buy smart software, but if standardisation has not been achieved, you are not scalable as an organisation.’ Plus, you also need to look at who is performing which tasks. Frank Biemans: ‘Where is expert knowledge really needed and where not? Is filling the cell a task for the machinist or logistics worker? Don’t calculate based on just manned and unmanned hourly rates; add another cheaper rate to fill the last few hours of the week with simple work.
Which product mix results in the most output?
Those who start using this KPI will soon see the focus shift in other areas. Frank Biemans: ‘Companies often still calculate the old-fashioned way: they look at how much processing time is required, multiply that by the hourly rate and that’s the price. It’s better to look at which product mix results in the most output in a week.’ In the current market, with more demand than supply and a shorter time to market for machine builders, lead time is often more important. A rule of thumb is that the higher the OPR is in the company, the shorter the lead time and the lower the cost. ‘That’s where the customer is best served,’ says Frank Biemans.
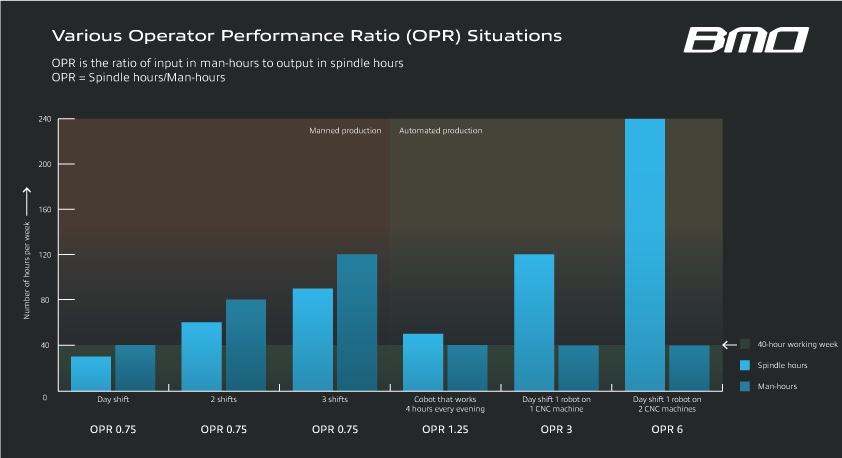
Up to €400,000 additional turnover per CNC machine
The OPR helps companies detect and solve such problems. Production managers using this KPI gain insight into how many man-hours are needed to meet a certain production level. ‘If you do a reference measurement, you can strive to improve a little each week.’ A calculation BMO Automation occasionally presents during discussions with clients shows the huge improvement potential. At an hourly rate of €60, compared to a machine that yields 1800 spindle hours per year, one that reaches 8760 spindle hours per year potentially yields around €400,000 of additional turnover on an annual basis. And with 140 production hours per week, lead time goes down from 5 weeks without automation to 2.5 weeks with automation. ‘Focus on OPR,’ advises Frank Biemans. ‘Otherwise, you certainly won’t achieve those hours of output with a mix of products.’
Benefits of Operator Performance Ratio
‘More spindle hours with the same number of operators is the solution to the shortage of skilled workers as well as achieving shorter lead times.’
- Better insight into required production capacity
- Potential of cutting lead time in half
- Up to €400,000 additional turnover per CNC machine
- A solution to staff shortages
- More spindle hours