For machine operators it is a challenge to each day configure again enough (small) series so that the CNC machines can run an entire night or weekend. Before there was the OptiVice our milling machine operators had to spend a lot of their time configuring the vices. Time that our operators did not have. On top of this, they also had to keep a watchful eye over all the configured vices. And even the smallest error of judgement could have consequences. What’s more, each vice took up space in the robot cell, which in turn takes up floor space.
And so in 2017, BMO started developing the optimal CNC vice: Self configuring, centric, electric, wireless and with a zero set-up time. Not an easy task, with a long period of trial and error. And so I’m very proud of the passion of the OptiVice team and the positive results of the practical tests.
Now operators can “OptiVice” set-up time to zero, bringing rest and flow into the milling process. The milling machine operator can now add extra value where it matters most. And more and smaller series can now be produced in a single unmanned run in one night or weekend (Multi-Batch). And this without having to configure a separate vice for each series. And without having to keep an eye over it. The OptiVice allows modern machinists to cope with personnel shortages by using the time of their CNC operators more efficiently.
“With the OptiVice, BMO is adding a new building block to the optimisation of its autonomous machining ecosystem.”
Frank Biemans, Founder van BMO
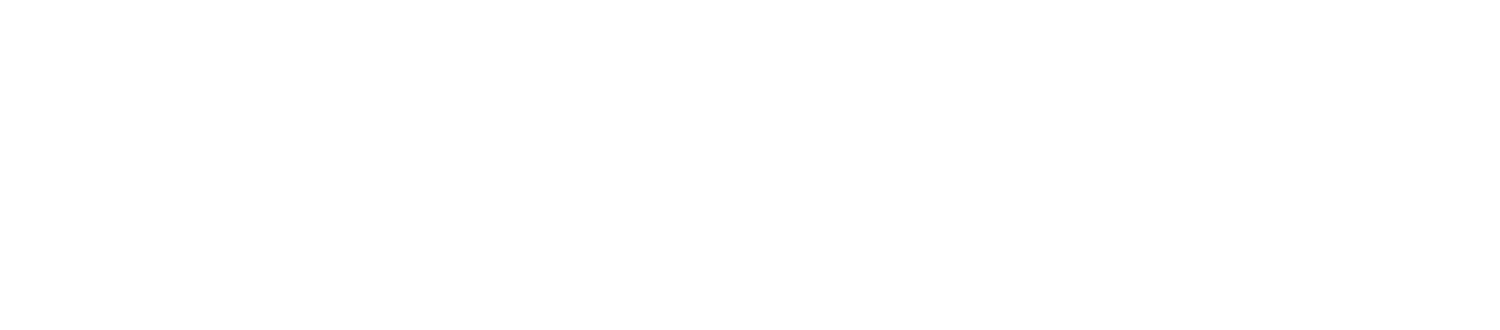