Schweizer Unternehmen Stabro AG produziert mit Titanium Serie rund um die Uhr
Die 10 Mitarbeiter starke Stabro AG ist das erste Schweizer Unternehmen, das in eine Automationslösung des niederländischen Herstellers BMO Automation BV (CH-Vertretung: Mikutec GmbH) investiert hat. Die versorgt ein DMU 60 EVO 5-Achs-Zentrum mit Rohteilen. Mit der Automationszelle können mannlos hochgradig prozesssicher wechselnde Kleinstserien über das Wochenende gefertigt werden.
“Während der Woche die Nacht mannlos zu produzieren reicht heute nicht mehr. Wir müssen auch das Wochenende mit bis zu 72 Stunden unbemannt fertigen können. Das sind unsere Herausforderungen und das ist der Grund, dass wir als Pionier das erste Schweizer Unternehmen sind, das in eine Automationslösung von BMO Automation investiert hat”
Obiges Zitat stammt von Marcel Dietsche, Inhaber und CEO der Stabro AG. Er hat den Beruf des Polymechanikers von der Pike auf bei Saurer (Lastwagenbau) gelernt und schon früh Erfahrungen sammeln können, dass Veränderungen in der Industrie die einzige Konstante ist. Mit der jüngsten Investition in ein flexibles Automatisierungssystem von BMO Automation BV des Typs Titanium 180 setzt die Stabro AG auf eine mehrfach international ausgezeichnete Automationslösung des niederländischen Herstellers.
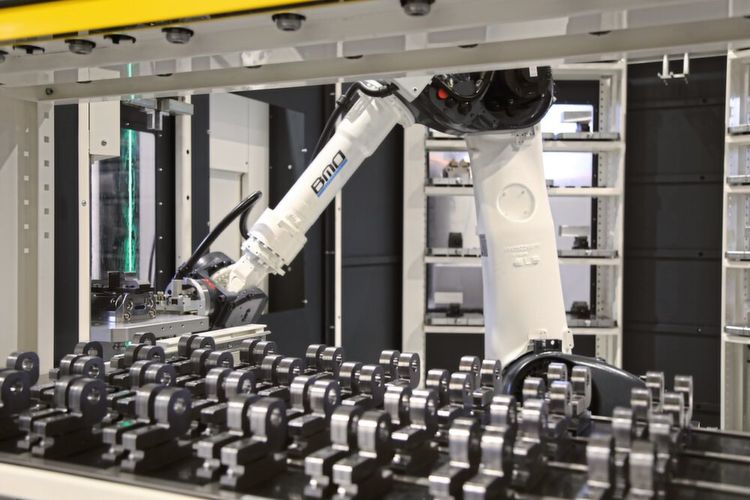
Stabro AG: Stärken im Fräsen kubischer Werkstücke
Die Stärken der Stabro AG liegen im Fräsen kubischer Werkstücke von Faustgrösse bis 600 × 700 mm Kantenlänge. Bearbeitet werden Materialien wie Alu, Stahl, Chromstahl und Kunststoffe. Der Schwerpunkt liegt bei Einzelteilen bis hin zu kleineren Serien von 10 bis 30 Stück. M. Dietsche: «Eine Losgrösse mit 100 Werkstücken ist für uns fast schon eine Grossserie.»
Die Aufträge kommen aus Automobilindustrie, Bahnwesen, Luftfahrt bis hin zur Medizinaltechnik. Die Kunden kommen überwiegend aus der Region Ostschweiz. Es gibt aber auch Kunden am Genfersee sowie in Polen als auch in Tschechien. Über die Kunden in Osteuropa ist M. Dietsche besonders stolz: «Das beweist, dass der Standort Schweiz absolut konkurrenzfähig sein kann. Das liegt natürlich nicht nur am Preis, dass wir unsere Werkstücke in diese Regionen liefern können. Das liegt im Wesentlichen an unserem Know-how, über das wir verfügen. Da haben wir am Standort Schweiz definitiv unsere Stärken. Der Preis muss natürlich auch stimmen, nicht zuletzt deshalb müssen wir in die Automatisierung unserer Werkzeugmaschinen investieren.
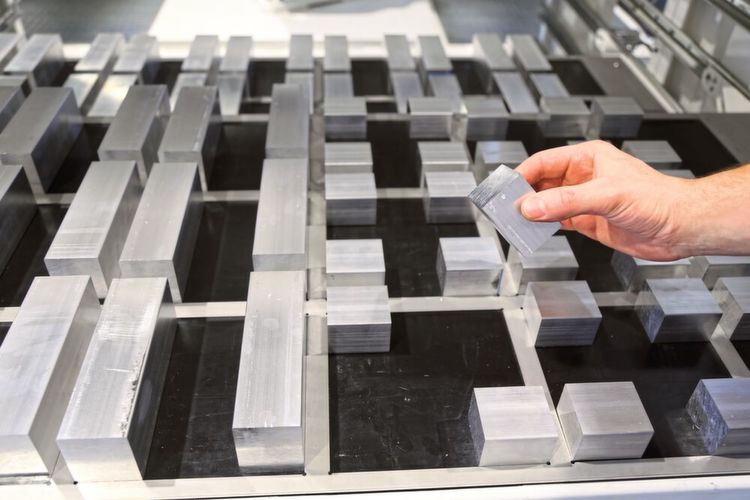
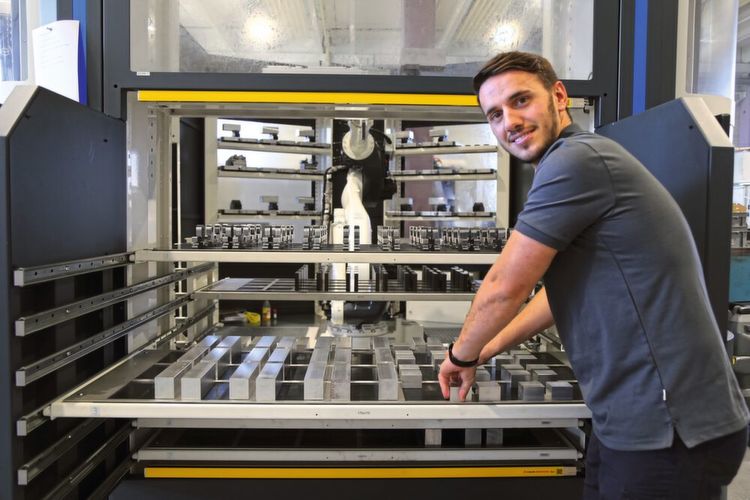
Hier im Bild gut zu erkennen, wie die Rohteile in die Schublade ins vorgegebene Raster eingelegt werden können. Die Schublade kann während der Hauptzeiten bestückt oder entladen werden.
Hochgradig flexible Fertigungslösungen gefragt
Aufgrund der kleinen Losgrössen musste die Produktion immer hochgradig flexibel agieren. Wegen des zunehmenden Kostendrucks musste die Auslastung der Spindellaufzeiten maximiert werden. M. Dietsche: «Grossserien lassen sich relativ einfach realisieren. Jedoch bei Einzelteilanfertigungen und Kleinserien gab es aus meiner Sicht lange Zeit keine Lösungen, die in einem guten Preisgefüge lagen und sich betriebswirtschaftlich rechneten. Das hat sich mit der BMO-Automationslösung relativiert.»
Michel Minikus (CEO, Mikutec GmbH): «Das ist das Stichwort: Eine flexible Automationslösung in einem guten Preisgefüge. Mit dem BMO-Automationssystem wird genau dieser Spagat realisiert. Und das ist auch der Grund, dass die BMO-Automationsanlagen bereits einige Industriepreise erhalten haben. Das Konzept ist so ausgelegt, dass sowohl Paletten als auch Rohteile per Knickarmroboter und Greifer gehandelt werden können. Darüber verfügt der Rohteile-Speicher über einen oder mehrere Voreinstellplätze (modular erweiterbar), auf dem die Rohteile und Fertigteile hauptzeitparallel be- oder entladen werden können. Das gilt nicht nur für die Spindel-Hauptzeit, sondern auch wenn der Roboter die Teile greift, lassen sich die Voreinstellplätze bedienen.»
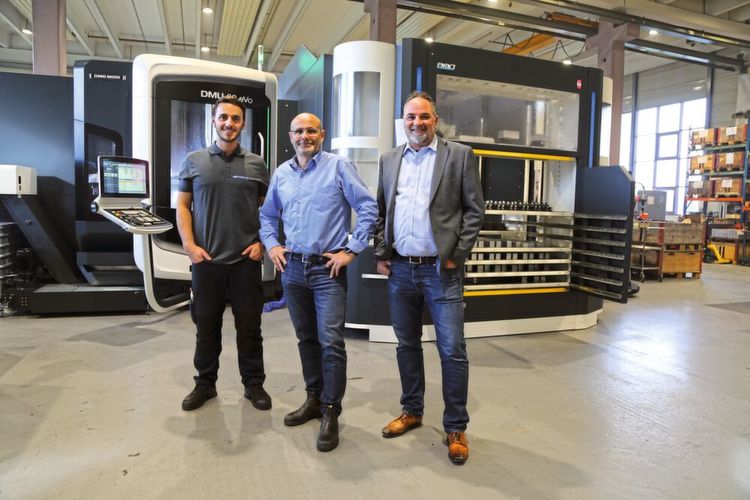
Bedienung: So einfach wie ein Toaster
Baton Kuqi (Produktionsleiter): «Entscheidend ist immer auch die Bedienung solcher Systeme. Idealerweise muss ein solches System so einfach zu bedienen sein wie ein Toaster. Gut, das ist vielleicht zu viel verlangt, aber hier muss ich BMO ausdrücklich loben.»
Dietsche ergänzt: «Selbst ich bin in der Lage das System auf eine neue Serie und ein neues Werkstückspektrum umzuprogrammieren. Ohne dass ich tagtäglich damit arbeite. Das ist in einem KMU, wie wir es sind, entscheidend. Wenn der zuständige Mitarbeiter wegen Krankheit oder Ferien ausfällt, sind alle anderen Kollegen in der Lage das System zu bedienen.»
Minikus: «Die niederländischen Entwickler wussten genau, was am Markt gefragt ist. Und sie wissen, dass eine einfache Bedienung eines der grössten Bedürfnisse innerhalb von Produktionsbetrieben ist. Natürlich muss auch alles andere passen. Prozesssicherheit, Grösse, Kostenstruktur, Software-Schnittstellen. Aber eine einfache Bedienung ist das A und O. Wer ein Smartphone bedienen kann, der kann auch diese Anlage bedienen.»
Dietsche bestätigt: «Wenn ich eine neue Kleinserie programmieren müsste, wäre es in fünf Minuten programmiert. Meine Maschinenbediener machen das noch schneller. Das ist wichtig. Sie müssen den Roboter nicht programmieren, das geht praktisch von allein. Das könnten sie auch gar nicht, sie wissen wie man ein CNC-Programm optimal auslegt. Das sind ihre Kompetenzen und genau hier kommt uns die BMO-Automation hervorragend entgegen. Besser kann man es nicht machen.»
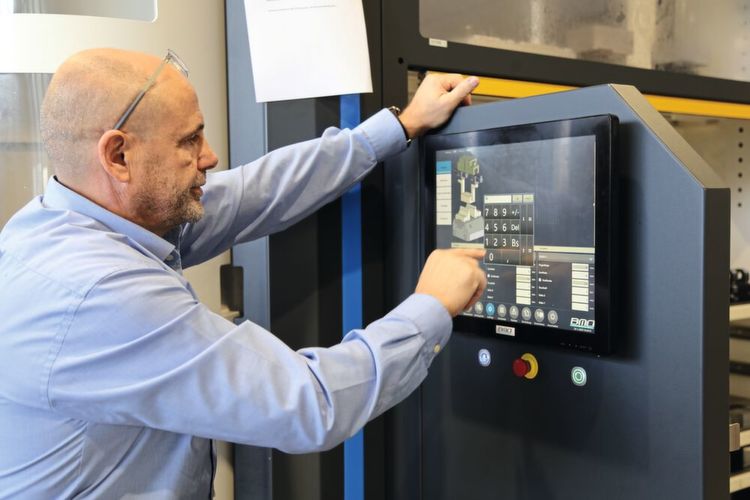
Titanium 180: Flexibles Automatisierungssystem
Bei dem BMO Titanium 180 handelt es sich um ein flexibles Automatisierungssystem mit hoher Kapazität sowohl bei der Rohteil- als auch bei der Palettenbeladung, um grössere und kleinere Serien flexibel zu automatisieren. Bereits in der Standardausführung können mehrere unterschiedliche Produktserien durcheinander automatisch geladen werden, ohne dass ein Bediener eingreifen muss.
Bei der Stabro AG werden sowohl Paletten als auch Einzelteile im System gelagert. Die Einzelteile werden in Schubladen auf einem Rastersystem einfach eingelegt. Der Titanium 180 kann mit sieben Schubladen bestückt werden. Bei Stabro wurde das System mit sechs Schubladen für die Einzelteil-Beladung ausgerüstet. Die Siebte kann Stabro zudem mit unterschiedlichen Serien beladen. Über die Softwaresteuerung werden alle weiteren Parameter eingegeben.
Darüber hinaus stehen der Stabro AG weitere 38 Palettenplätze (à 395 × 395 mm) zur Verfügung, die per Nullpunktspannung in die Maschine per Roboter geladen werden. Auf den Paletten werden typischerweise grössere und schwerere Werkstücke ab 15 kg gespannt, die für den Greifer nicht geeignet sind.
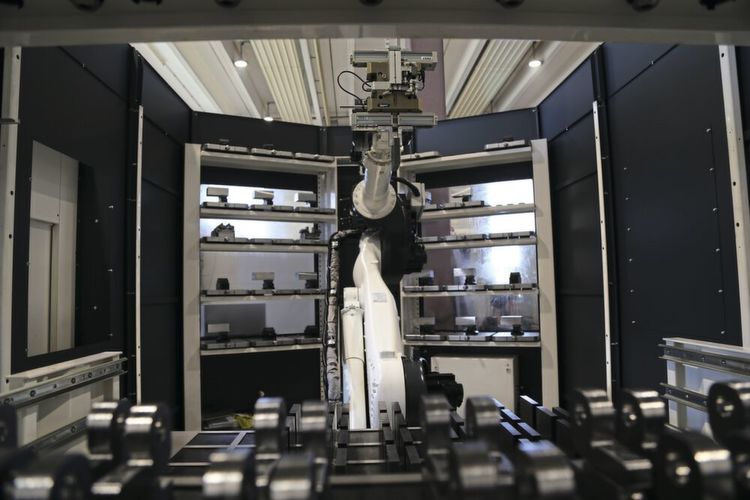
Exkurs: Spanntürme
Auf die Frage, ob das System auch mit Spanntürmen arbeiten kann, antwortete M. Minikus: «Generell sind Spanntürme in das System integrierbar. Die Automationslösung ist hierfür entsprechend ausgelegt. Aber es muss Sinn machen, um Spanntürme zu integrieren.»
Dietsche «Ich kann dazu aus unserer Erfahrung etwas sagen. Wir haben bereits bei einem Horizontalbearbeitungszentrum Spanntürme im Einsatz. Das ist durchaus interessant, um mehrere Bauteile effizient zu bearbeiten. Aber auf unserer BMO-Anlage machen Spanntürme keinen Sinn. Denn bei einem Spannturm muss jedes Werkstück manuell eingespannt werden, was mehr oder weniger Aufwand bedeutet. Das, was wir am Turm manuell machen müssten, besorgt die BMO-Anlage und die Werkzeugmaschine mit automatisiertem Spannstock vollautomatisch. Das ist ein absolutes Plus. Gleichwohl kann es Anwendungen geben, wo Spanntürme ggf. geboten sind, auch bei der BMO-Anlage. Aber bei einem Vertikalzentrum, wie wir es im Einsatz haben, kommt das klar nicht in Frage.»
Das Greifersystem
Das System verfügt über einen 6-achsigen Knickarmroboter. Der Greifer ist ein modifizierter Schunk-Standardgreifer, der dank einer BMO-Erweiterung über eine grosse Spannweite von 0 bis 250 mm verfügt. Damit sind mit ein und demselben Greifer sowohl kleinere als auch grössere Werkstücke ‚handelbar‘. Zusätzlich ist das System mit Greifern für unförmige und runde Werkstücke ausgerüstet. Damit können alle zu produzierenden Werkstücke ‚gehandelt‘ werden. Der Standard-Roboter ist für Werkstückgewichte bis zu 180 kg ausgelegt, Sonderlösungen gehen bis 500 kg.
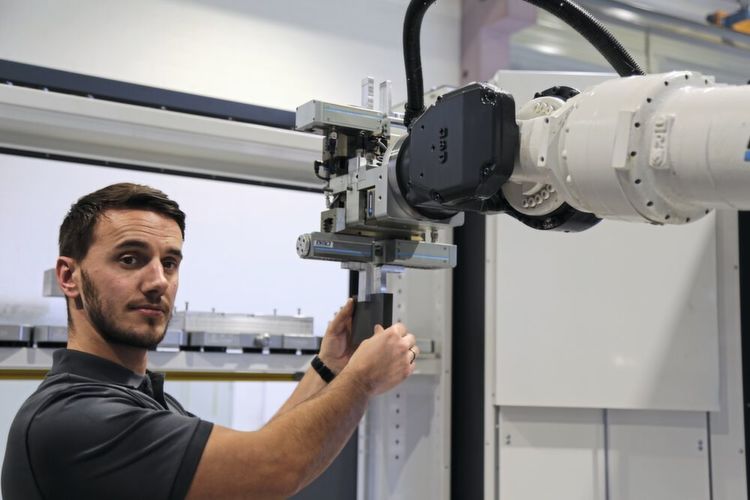
Fertigungsbearbeitung problemlos machbar
Minikus: «Dank einer Wendestation ist die Rückseiten-Bearbeitung der Werkstücke voll automatisiert. Das läuft so: Der Roboter entnimmt das einseitig bearbeitete Werkstück, legt es auf der Wendestation ab, greift das Teil um und führt es in das automatische Spannsystem für die Rückseitenbearbeitung.»
Kuqi ergänzt: «Nach der Rückseitenbearbeitung wird das fertige Werkstück in die Schublade zurückgelegt. Eins nach dem anderen. Auch am Wochenende, wenn unsere Mitarbeiter frei haben. Das ist eine recht geniale Lösung.»
Wichtig: Genügend grosser Werkzeugspeicher
Damit die unbemannte automatisierte Fertigung von wechselnden Kleinserien reibungslos vonstatten geht, müssen darüber hinaus noch einige Randbedingungen erfüllt sein. Wobei die Randbedingungen eine sehr zentrale Rolle spielen.
Dietsche: «Wir benötigen für einen Grossteil der Fräs- und Bohrwerkzeuge Schwesterwerkzeuge, die entsprechend eingewechselt werden können, sobald die Standzeit erreicht ist. Die DMU verfügt über 120 Werkzeuge, das hat sich für uns bisher als ausreichend für die automatisierte Fertigung herausgestellt.»
Obendrein muss der Spänefluss gewährleistet sein. Derzeit klappt das auch über das Wochenende mit einer Mulde. Das ist aber abhängig vom Zeitspanvolumen und die Späneentsorgung muss entsprechend dem Spanvolumen ausgelegt werden. Darüber hinaus fahren wir die Schnittwerte bei den unbemannten Schichten runter. An die Grenze der Werkzeugleistungen kann man bei bemannten Schichten gehen, bei unbemannten Schichten ist Prozesssicherheit oberste Priorität.
Weitere Werkzeugmaschinen integrierbar
Auch an die Zukunft ist gedacht, wie M. Dietsche bestätigt: «Wir planen, eine weitere Werkzeugmaschine an das BMO-Automationssystem anzubinden. Dabei könnten wir problemlos einen anderen WZM-Hersteller integrieren. Das ist für das BMO-System völlig offen bezüglich Schnittstelle. So können wir die Produktivität noch weiter steigern. In Zukunft wird es bei uns keine Maschinen-Investition mehr geben ohne Automation.»
Ein Ausschnitt aus dem Werkstückspektrum, das von der Stabro AG produziert wird.
Stabro AG
Das 10 Mitarbeiter starke Fertigungsunternehmen Stabro AG wurde in 2009 von M. Dietsche übernommen. Seitdem investiert er kontinuierlich in den Maschinenpark und Automationslösungen. Seine Ausbildung zum Mechaniker machte M. Dietsche bei Saurer. M. Dietsche lernte im Bereich der Saurer-Lastwagenfertigung und wechselte in die Montage des Textilmaschinenbaus. Anschliessend investierte M. Dietsche in diverse Weiterbildungen und nahm seitdem Führungspositionen in der Industrie ein.
Stabro AG
Hofstrasse 22
8590 Romanshorn